LESS MATERIAL NEEDED TO PRODUCE SEALING FILMS
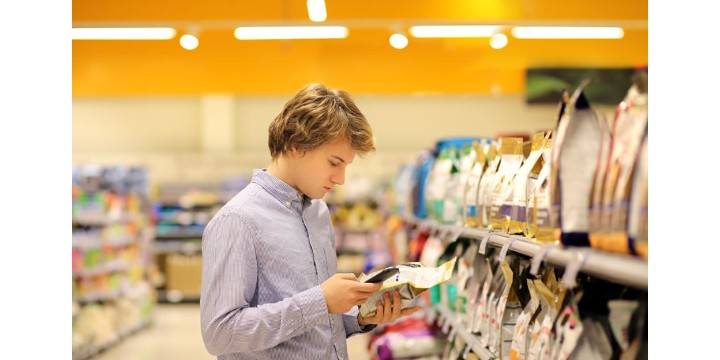
One function of packaging is product safety; this may indeed be its most important function. It is therefore important that packaging for food or liquid goods is firmly sealed so that the product will not come into contact with unwanted substances or accidentally leak out of the packaging. Polyolefin-based sealing films are a tried-and-tested packaging material.
A solution for producing them that requires much less material has now been implemented by the Dutch company Plasthill, a subsidiary of the Oerlemans Packaging Group, in cooperation with the Constantia Flexibles Group GmbH from Austria. The film, called CompresSeal, according to the company has a greater seal strength than classic polyethylene foils, while simultaneously requiring less material for production and therefore reducing weight by up to 30 %.
MICRO-EMBOSSING TECHNOLOGY MAKES WEIGHT REDUCTION POSSIBLE
Pim Vervaat, CEO of Constantia Flexibles: "The technology behind our CompresSeal film is the result of years of research and development by our experts. Together with Plasthill's expertise in embossing, we are taking this pioneering packaging solution to the next level and are offering it to customers for a variety of applications.”
The CompresSeal technology is said to rely on a novel specialised micro-embossing technique. The embossing pattern is said to enable a weight reduction of up to 30 % per m2 of polyolefin-based sealing films at the same measured thickness. This technology thus helps to reduce the CO2 emissions of packaging as well as the consumption of raw materials.
PROCESSABILITY STAYS THE SAME IN SPITE OF LESS ADDITIVES
The new film from this Dutch-Austrian cooperation has yet another advantage, says the manufacturer: During production, far less migrating lubricant is said to be used compared to conventional PE and PP films. These additives are necessary to simplify the handling of the films during processing, in order to make sure they will not stick to machines or to make unrolling them easier. At the same time, these migrating lubricants can cause colours, for example, or other coatings of the film to come off to some extent. The technology developed now requires less additives, yet the coefficient of friction of the packaging line remains constant, regardless of environmental factors like temperature and humidity.
Sander Kool, CEO of Plasthill Technical Films: "This sustainable innovation, the production of the new films, reflects our Rethink Plastics strategy. The cooperation and teamwork with Constantia Flexibles was great!"
This packaging solution is especially apt for flowpacks, for example for detergents, dry pet food, coffee, nuts and savoury foods, as well as for stand-up pouches containing liquids. Development is now set to focus primarily on polyethylene foils with a thickness of over 60 grams per square meter, where saving weight has the biggest effect on the environment.
Comentarios